Jamie Agombar formed part of a team who visted NUS' Fairtrade clothing company's, Epona's, factories in India and Bangladesh. Here, we look back at his thoughts.
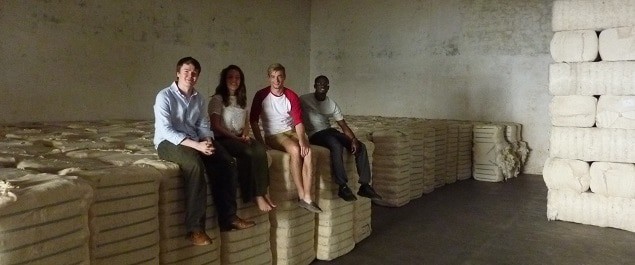
Today we visited the factory's spinning mill, which is about an hour's drive outside of Coimbatore, deep in rural southern India. The site comprises one very large, quite modern factory building, with a dormitory and canteen block out the back. The site is home to 380 residential workers who have come here to work, mostly from the Orissa region. The staff work an eight hours shift each day, six days a week, and there are three shifts a day, providing 24 hour production.
We were surprised to find out that staff in the spinning mill are not subject to the same level of Government minimum wage as those in their main factory. We were told that staff here earn about 65,000-70,000 Rupees a year (£930-£1000 per annum), with that being is their take-home pay, as they do not earn enough to pay tax. They also get their accommodation and food for free on top of their salary. Unlike their main factory, which had posters in most rooms celebrating their plans to pay a living wage, this site had no such posters. The company will need to substantially increase the amount they pay here to a living wage if they are to succeed in being one of the first in India to get the Fairtrade Textile Standard. Despite the low pay, the staff seemed to be in good spirits, and friendly, and it had all good feel to it. I've visited other factories where, when people forget you are there, workers are snapped at, bossed around, and treated like subordinates, but that didn't seem to be the case here at all.
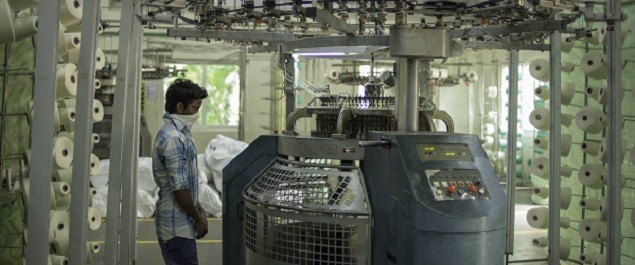
You couldn't help but be impressed by technical processes that we saw in the factory, mostly German machinery that is so complex it was difficult to comprehend how it could work. The cotton bales are stripped down by an automatic machine, like a giant grazing hoover. The cotton is then sucked away to another room, where it is screened and cleaned, before going into a machine that makes it into hundreds of a seemingly never-ending inch-wide cotton sausages, which are automatically coiled into large barrels. From there it is stretched and wound several times, each time getting thinner and stronger. Eventually the cotton sausages have become a thread of cotton as we know it. The factory produces 14 tonnes of cotton thread a day, and we worked out that this equated to 43,095 miles cotton a day, enough to go around the world 1.7 times.
The final third of the factory is used for weaving, where space-age machines automatically combine cotton from dozens of reels of thread to make fabric. This is the end stage for this factory, and the giant rolls of cloth are now ready to go to the dye house, and then on to the manufacturing factory that we visited yesterday.
As we left the factory, we reflected on how the process was almost entirely automated, with the staff seemingly just being there to keep the machines fed and running correctly. They are machine operators, like their peers in the other, affiliated factory (who operate cutting, sowing and printing machines), and this made us again question why they should earn less just because they are in a different part of the industry.
Compared to workers' rights, the factory's sustainability credentials were straightforward and unequivocally impressive. Yesterday we were shown their waste water treatment plants in their main factory. One treated sewage, and the other treated printing waste water. The former is impressive, because we saw many open sewers in and around Coimbatore, and it felt that the factory was going over and beyond what they needed to do. The latter was just as impressive, with a filtration system stripping out printing sludge, which then goes off for use in the cement making industry. It might be that factories are required to do this, but it was nonetheless impressive given the state of India's infrastructure.
Our colleagues from Fairtrade told us how there used to be 750 dyeing factories in and around Tirapur, most of which discharged polluting water into rivers. The local government gave them notice to improve voluntarily, but they didn't. So a few years ago it took sudden, drastic action and closed them all. The industry quickly bounced back, and now there are about 100 dyeing factories clustered together and sharing joint-venture waste water treatment facilities, all of them purportedly operating on a zero discharge basis. Whilst this is good, the rivers we saw in Coimbatore are in a truly shocking state, with them being used as general community rubbish dumps for all types of domestic waste, and contamination from domestic sewage.
On a much more upbeat note, we were shown an impressive one-megawatt solar array, covering six acres. I've seen solar in many cloudy western countries, but this was different - there was barely a cloud in the sky, and it is like this for much of the year in this part of India. The panels are productive, producing 12-15% of all the electricity consumption of the spinning mill, which is an awful lot of energy given how automated the factory is.
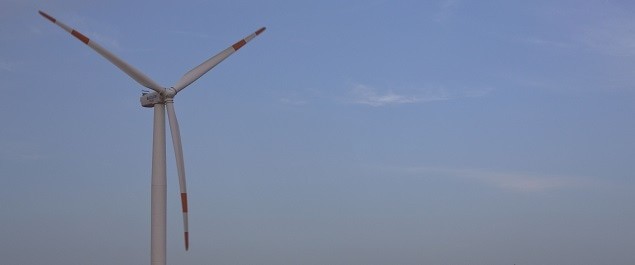
Better still, the factory has built 18 one-megawatt wind turbines way off to the south of the factory. It sells the energy into the grid, but this generation, together with the solar, means that this factory is a net contributor of energy to the grid, producing 30% more electricity than they use, through 100% renewables. This is an amazing feat; I don't know of any UK universities or companies that have achieved it. Those that come close to carbon neutrality buy green energy or offset emissions - but this was the real deal. India is not an easy place to make things happen in, there is plenty of bureaucracy, and some corruption, so it is definitely hats off to this factory for being energy positive.
On recycling, the company makes uses of pretty much all of their waste yarn, fabric and off-cuts. The yarn is re-spun and re-blended, and the waste cotton is manufactured into a range of useful products, such as the swing tags that we have on our Epona clothes.
We also learnt how the polyester they use in the cotton-ply blends is made from old plastic bottles. The process happens in another company (the factory we use just buy the product) but it involves PET bottles being shredded, melted down and spun into polyester. This by itself would be good, but you have to remember that the factory is in fact producing Fairtrade and organic cotton, blended with polyester from recycled waste, made using renewable energy.
It has been an amazing week, and we feel privileged to have met such wonderful people, and to have seen so much of this amazing country. What is very clear us that our Epona clothing is something we should all be proud of. From the Fairtrade price guarantees for the farmers, and the Fairtrade premium projects in the school and farms, to the living wage commitments and environmental credentials, our clothing company, Epona, is making a positive difference, and we should all be proud of that.